Understanding The Dangers of Bearing Fluting From VFDs

There are a lot of reasons to embrace Variable-Frequency Drives (VFDs). These drives allow you to precisely control the speed of attached motors by modulating the input power before it’s passed on to the motor. In turn, you gain substantial flexibility in how you use the motor, as well as reducing startup energy use and opening up new opportunities for optimizing power usage overall.
However, VFDs do have one downside. Due to how they operate, they can easily send stray current down the drive shaft, into the engine, and, typically, into the bearing compartment. This current can cause significant damage to the bearings, called bearing fluting, which can ruin the motor without preventative measures.
What Is Bearing Fluting and What Causes It? VFDs work by taking an AC input, then converting it to DC. This DC is then sent through insulated gate bipolar transistors (IGBT), which convert it back into AC as a series of voltage pulses. However, the IGBTs and drive controller can precisely fine-tune the current’s phase and control the speed of the motor in this way.
The problem is the rapid voltage shifting of the IGBTs creates a parasitic capacitance between the motor’s stator and rotor. This causes unwanted voltage, called common mode voltage, to enter the motor shaft. Once there, the bearing compartment is typically the fastest path to the ground, so the voltage enters the motor.
Without any shielding or protection, standard bearings are electrically conductive. As voltage builds up in the bearing compartment, tiny electric arcs jump between the bearings and the compartment’s walls. Each arc causes micro-pitting on the surface it contacts. So, the bearings become increasingly rough – taking on a frosted appearance – and the bearing raceway develops a pattern of evenly spaced grooves like a washboard.
This is bearing fluting.
The damage is invisible from the outside but builds up over time. Eventually, you’ll start to notice distinctive humming or buzzing sounds from the bearings interacting with the “washboard” raceway. Unfortunately, by the time the problem is noticeable, it’s also too late to fix. Once you know you have a bearing fluting problem, the bearings, and possibly the entire motor, will have to be replaced.
The best method of preventing bearing fluting is using inductive absorbers, such as CoolBLUE, to absorb the stray current. CoolBLUE inductive absorbers are inexpensive and simply clamp onto the power lines. They typically take five minutes or less to install and are a fire-and-forget solution that will last for the life of the VFD.
Should absorbers not be a practical solution, such as in tight containment spaces, other alternatives exist. The motor shaft itself could be physically grounded. Or, more commonly, the issue is addressed within the bearing compartment. Non-conductive ceramic bearings will prevent fluting problems, as will conductive grease intended to route the common mode current straight to the ground.
If you’re having issues with VFD voltage concerns or bearing fluting, AES can help. Reach out to our team to discuss the problem.
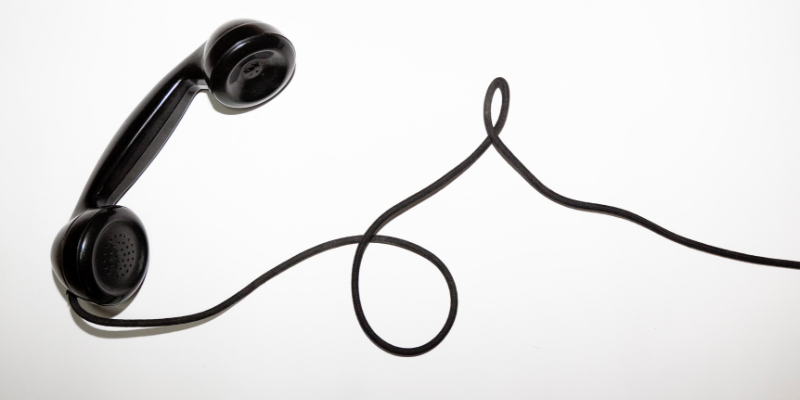
