How to Fix a Hydraulic Pump: A Guide for Beginners
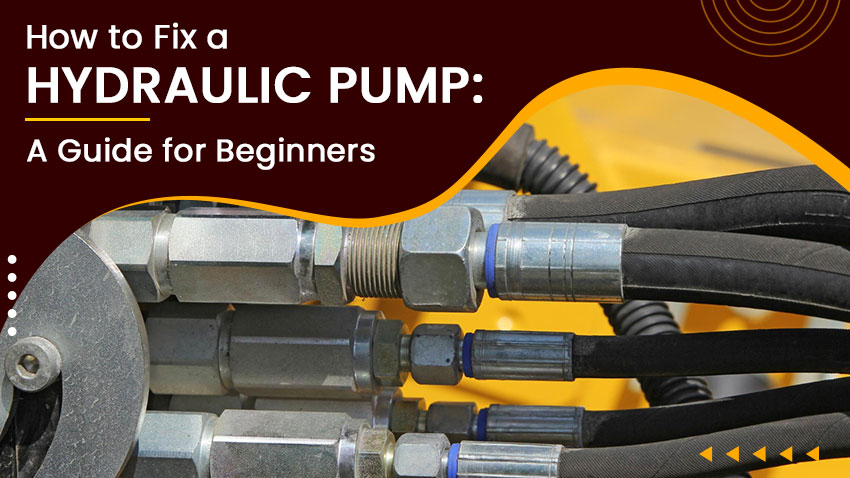
How to Fix a Hydraulic Pump: A Guide for Beginners
Hydraulic pumps are integral components for many pieces of machinery and industrial equipment. And, like any mechanical device, these hydraulic pumps can encounter issues over time, such as pressure loss, fluid leakage, or unwanted noises.
Identifying and fixing these issues quickly is vital for avoiding costly downtime and maintaining smooth business operations. In this blog, we will walk you through the step-by-step repair process to help you effectively troubleshoot and repair hydraulic pump issues as they occur.
What Are the Different Types of Hydraulic Pumps?
To effectively fix hydraulic pump issues, it’s important first to understand the types of pumps that are regularly used because each type has its own unique qualities and applications. Let’s look at a few types:
1. Piston Pumps:
Piston pumps are known for their high efficiency and reliability. They use reciprocating pistons to pressurize the hydraulic fluid, making them ideal for applications requiring high pressure and precise conztrol.
2. Vane Pumps:
Vane pumps are simple and cost-effective pump systems, consisting of rotating vanes that create pressure by trapping and releasing fluid between the vanes and the pump housing. These pumps are widely used in industrial and mobile hydraulic systems.
3. Gear Pumps:
Gear pumps are the simplest type of hydraulic pump, making them popular for a multitude of applications. They consist of meshed gears that transfer fluid from the inlet to the outlet and are known for their durability and affordability.
Why Do Hydraulic Pumps Fail?
Understanding the common causes of hydraulic pump failure is crucial for effective troubleshooting. Here are a few common causes of hydraulic pump failure:
1. Fluid Contamination:
Fluid contamination is one of the primary reasons for hydraulic pump failure. Contaminants such as dirt, debris, and moisture can impair a pump’s performance and damage its internal components. As such, maintaining clean hydraulic fluid and regularly inspecting and replacing filters are essential.
2. Cavitation:
Cavitation occurs when the hydraulic fluid experiences low pressure, forming vapor bubbles. These bubbles collapse rapidly, resulting in shockwaves that can erode pump surfaces and hinder their operation. Proper fluid levels, unrestricted flow, and correct pressure are essential to prevent cavitation.
3. Excessive Temperature:
Operating a hydraulic pump at high temperatures can cause premature wear and failure of its components. Excessive heat can lead to fluid degradation, seal failure, and reduced pump efficiency. It’s important to monitor and control the operating temperature of the hydraulic system through cooling measures if necessary.
4. Uncorrected Leaks:
Leaking hydraulic connections or damaged seals introduce air into the system, reducing pump performance and increasing the potential for failure over time.
How to Repair Your Hydraulic Pump
Repairing a hydraulic pump requires careful inspection and a basic understanding of its components. Follow these steps to fix common issues:
1. Identify the Problem:
Identify the specific issue with your hydraulic pump, such as pressure loss, unusual noise, or fluid leakage. This initial diagnosis will guide your repair process.
2. Shut Off the System:
Before performing any repairs, ensure the hydraulic system is turned off, and the pressure is relieved to prevent accidents or injuries.
3. Inspect for Leaks:
Thoroughly check all connections, fittings, and seals for signs of leakage. Replace any damaged components and ensure all connections are properly tightened.
4. Clean the System:
If fluid contamination is suspected, flush the hydraulic system thoroughly and replace the fluid with clean, recommended hydraulic oil. Regularly maintain clean filters to prevent future contamination.
5. Check the Filters:
Inspect and clean or replace the filters to ensure proper fluid filtration and prevent further contamination. Regular filter maintenance is essential for optimal pump performance.
6. Address Cavitation Issues:
If cavitation is identified, check the system for any restrictions, blockages, or incorrect fluid levels. Address these issues and ensure proper fluid flow to eliminate cavitation.
7. Monitor Temperature:
Regularly monitor the operating temperature of the hydraulic system. If excessive heat is detected, consider installing additional cooling measures or addressing any underlying issues causing high temperature.
8. Seek Professional Assistance:
If you encounter complex or major pump issues during the repair process, it’s recommended to seek help from a professional hydraulic technician to ensure proper repairs and prevent further damage.
Need Help? Let Professionals at AES International Do the Job!
Repairing a hydraulic pump can be a challenging task, and you’ll want to seek out professionals that can quickly diagnose and resolve a wide range of hydraulic issues.
AES International is proud to be your first choice for hydraulic pump repair. Our trained professionals have the expertise to identify and fix your pump issues promptly, providing you with peace of mind and reliable performance.
Contact AES International at (866) 386-1001 for all your hydraulic pump repair needs. Our dedicated team will work closely with you to restore your pumps to optimal condition. Don’t let the complexities of hydraulic pump repair overwhelm you, trust AES International to make sense of it all.
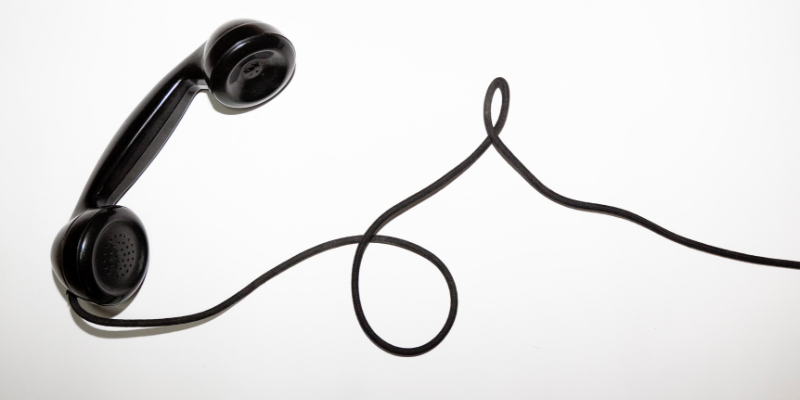
